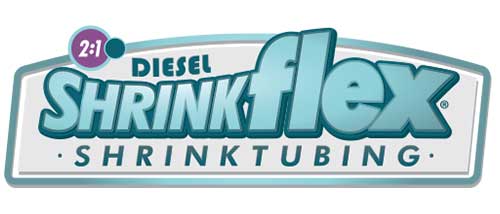
2:1 Diesel Resistant Heatshrink
Resists Diesel Fuel and Corrosive Chemicals
Diesel resistant heat shrink tubing is the most widely used heat shrink in aviation, racecar and other applications where highly corrosive fuels, fluids and oils are used. Its high resistance to aviation and diesel fuels, hydraulic fluids and lubrication oils makes it suitable for protecting military ground cables and harnesses from both these fluids, and abrasion. Diesel resistant heat shrink reliably protects terminals, connectors, and other components from most industrial fuels and mechanical damage.
The 4mm wall thickness resists damage from abrasion and flying debris, and stays secure even at elevated temperatures. The 2:1 shrink ratio allows easy installation over plugs and connectors, and shrinks to a tight and flexible seal for protection of wires and connectors.
Shrinkflex® diesel resistant shrink tubing is available in diameters up to 2" in Black only.
- SHRINK RATIO: 2:1
- SHRINK TEMP: 347°F (175°C)
- COLORS: Black
- Stays Tight In Elevated Temperatures
- Remains Flexible When Shrunk
- Resists Diesel & Common Automotive Chemicals
- 4mm Thickness Provides Abrasion Protection
Polyolefin: This is the most commonly used heat shrink material and works for most heat shrink applications. Polyolefin comes in a variety of colors, sizes, shrink ratios, and has an operating temperature of -67° F to +275° F. Keep in mind, Polyolefin has a low tolerance for UV resistance compared to other shrink tubing.
PVC: Polyvinylchloride, or PVC heat shrink, is an economical solution ideal for lower temperature applications like food & beverage use. It also has a higher UV resistance than standard Polyolefin.
Fabric: Fabric heat shrink tubing is constructed using a combination of polyolefin and polyester. Fabric shrink is ideal for use in environments were retaining strength & abrasion resistance is important. This material often has a narrower operating temperature range as well as more longitudinal shrink than other shrink tubing materials.
PTFE: Polytetrafluoroethylene, or PTFE, is intended for use in applications where it is frequently exposed to very high temperatures. This material has a very high shrink temperature, making it difficult to shrink for most users without specialized heating equipment.
Kynar: Kynar heat shrink is highly flame retardant, abrasion resistant, and geared towards environments that require strain relief such as soldered connections and splices.
Viton: This shrink tubing is a fluid resistant, flame retardant flouro-elastomer with high solvent resistance intended for use in applications exposed to corrosive materials or high temp environments.
You have to be a bit careful when measuring for heatshrink because – as you may have guessed – heatshrink shrinks! When it comes to picking the proper size heatshrink, two important terms to remember are nominal diameter and shrink ratio.
Nominal diameter is the original or ‘unshrunk’ diameter of a piece of heatshrink. Shrink ratio is the approximate maximum amount that heatshrink will shrink relative to its nominal diameter. For example, heatshrink with a 1/4” nominal diameter and a 2:1 shrink ratio will shrink to a diameter of approximately 1/8”.
Measure the diameter of the cables you’re covering, including any attached connectors. Then, choose a heatshrink option with a nominal diameter greater than the diameter of your cables AND a shrink ratio that will ensure that the post-shrinkage diameter of the heatshrink is smaller than the diameter of your cables.
STEP ONE:Measure the Shrinkflex® shrink tubing to length and cut with a scissor. The thickness of your bundle, as well as the desired final appearance, will determine the length of the tubing you cut. Generally, a piece 1 1/2” - 2” long will accommodate almost any need. Single wires, or smaller bundles, require shorter pieces.
STEP TWO:Slip the Shrinkflex® heat shrink tubing over the bundle and position it so that both the sleeved and unsleeved portions are sufficiently covered. Notice the small pieces of tubing in- stalled on single wires as part of a color coding system. If your project requires multiple operations, always work up from the smallest to the largest bundle.
STEP THREE:Gently apply heat to Shrinkflex® heat shrink tubing from a heat gun, hair dryer or torch with an appropriate attachment. Keep the heat source far enough away so that hot metal or direct flame does not come in contact with the tubing, wires or sleeving. Move the heat around the bundle to prevent damaging the sleeving and to ensure that all areas of the tubing have been shrunk. Once cooled, your installation is complete.