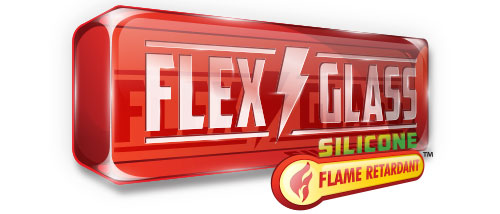
FR Silicone Flex Glass® Grade C
Silicone Coated Fiberglass Sleeving
Flame Retardant Silicone Flex Glass® sleeving is an extremely flexible braided fiberglass sleeve coated with a flame retardant elastometric silicone rubber sheath.The unique self-fitting construction allows SF sleeving to expand slightly for easy installation, and provides a snug fit for minimum movement and reduced internal abrasion. SF sleeving is rated to 392°F. (Class H), is abrasion resistant, and maintains it’s flexibility in low temperature environments. It is available in a very wide range of sizes, and is ideal for use in appliance assemblies, wire harnesses, transformer leads, power supplies, motor coil and heater leads.
Why Is Insulating Wires Important?
Safety: Insulating wires helps prevent electrical shock and electrocution by creating a barrier between the electrical conductor and anything or anyone that may come into contact with it. This is particularly important in high-voltage applications where the risk of injury is greater.
Prevention of short circuits: Insulation helps prevent short circuits, which can lead to fires, equipment damage, and electrical hazards.
Protection of equipment: Insulating wires helps protect electrical equipment from damage caused by exposure to moisture, dust, chemicals, and other environmental factors.
Efficiency: Insulating wires can help improve the efficiency of electrical transmission by reducing the amount of energy lost through leakage.
Compliance: Insulating wires may be required by regulatory agencies or building codes to ensure compliance with safety standards.
How to Choose The Correct Braided Sleeving
A lot of factors go into determining the correct braided sleeving wire protection method for your project. We’ve broken it down to help you narrow your search:
- Operating Temp: Is your wire harness going to be regularly exposed to extreme temperatures or possible flames? The operating temperature of your harness is a critical consideration when choosing sleeving to ensure that the sleeving you select can withstand the intended environment and provide adequate protection.
- Flexibility & Expansion Ratio: Flexibility is an important factor if your wire harness will be snaking around a lot of corners or curves or is frequently moving. Expansion ratio refers to the amount by which the diameter of a braided sleeving can increase when stretched. The expansion ratio of braided sleeving can vary depending on the material it is made of and the construction of the braiding.
- Material: Braided sleeving is available in a wide range of materials to provide different levels of abrasion, UV, and chemical resistance. Material also effects wire harness weight, EMI protection, and flexibility.
- Cutting Tool: Checking the recommended cutting tool for a sleeving product allows you to ensure you have the tools necessary for the job. If using a hot knife is not feasible for you, be sure to look for sleeving options that can be cut fraylessly with scissors.
- Sleeve Vs. Wrap: If you are consistently changing the wires & cables of your harness then a split wrap may be a better option for you than a solid sleeving product to installation is fast & easy.
- Industry & Environment:Techflex® braided sleeving products are organized into categories based on the most common uses of each product. If you work in a specific industry, visiting the corresponding product category may be a fast way to see applicable sleeving options for your project.
- Color choices: Braided sleeving is great for matching, color coding, and to identify wires & cables. If color coding is your goal, make sure the product you are considering offers enough colors for your project.
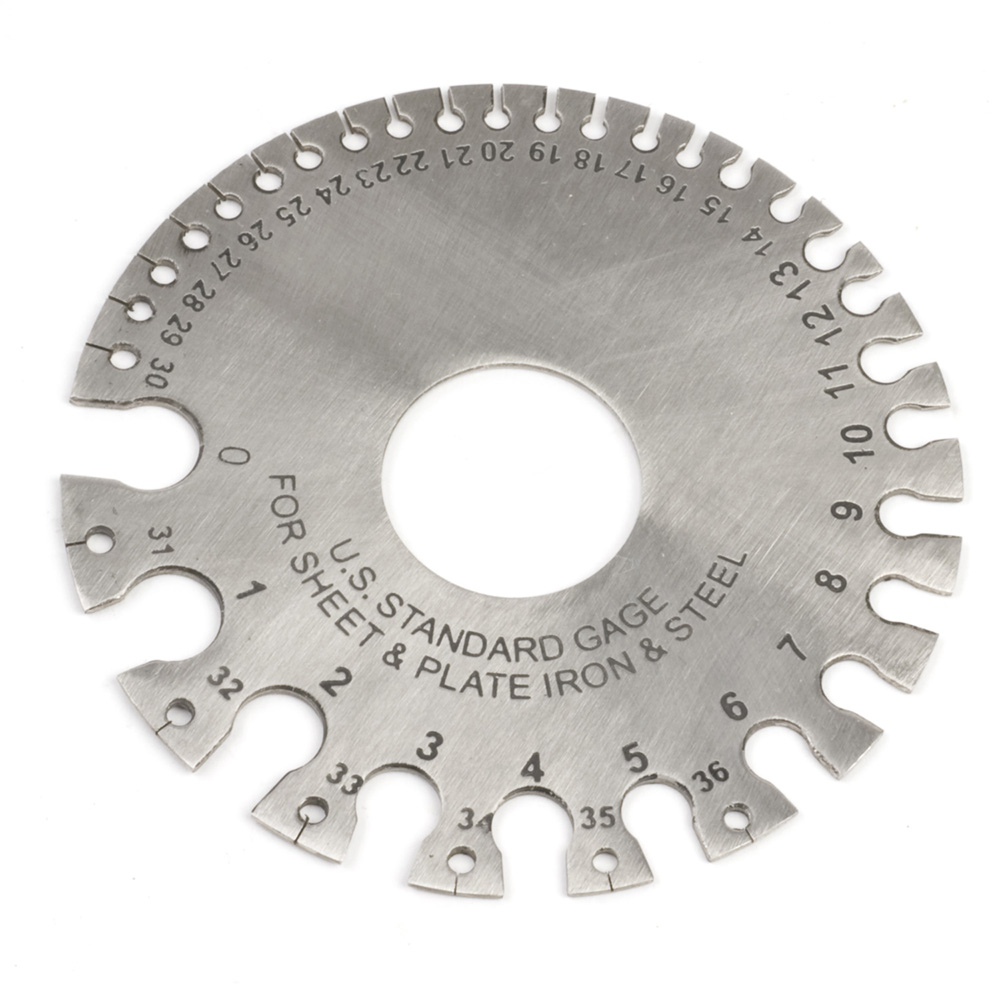
What is AWG (American Wire Gauge)?
The American Wire Gauge (AWG) is a standard for measuring the size of electrical wire in the United States. It is a method for determining the cross-sectional area of a wire, which is expressed in units of circular mils (one mil is equal to one thousandth of an inch).
AWG is a standardized system that assigns a specific number to each wire size based on its diameter. The larger the wire diameter, the smaller the AWG number. For example, a 10 AWG wire has a larger diameter than a 16 AWG wire.